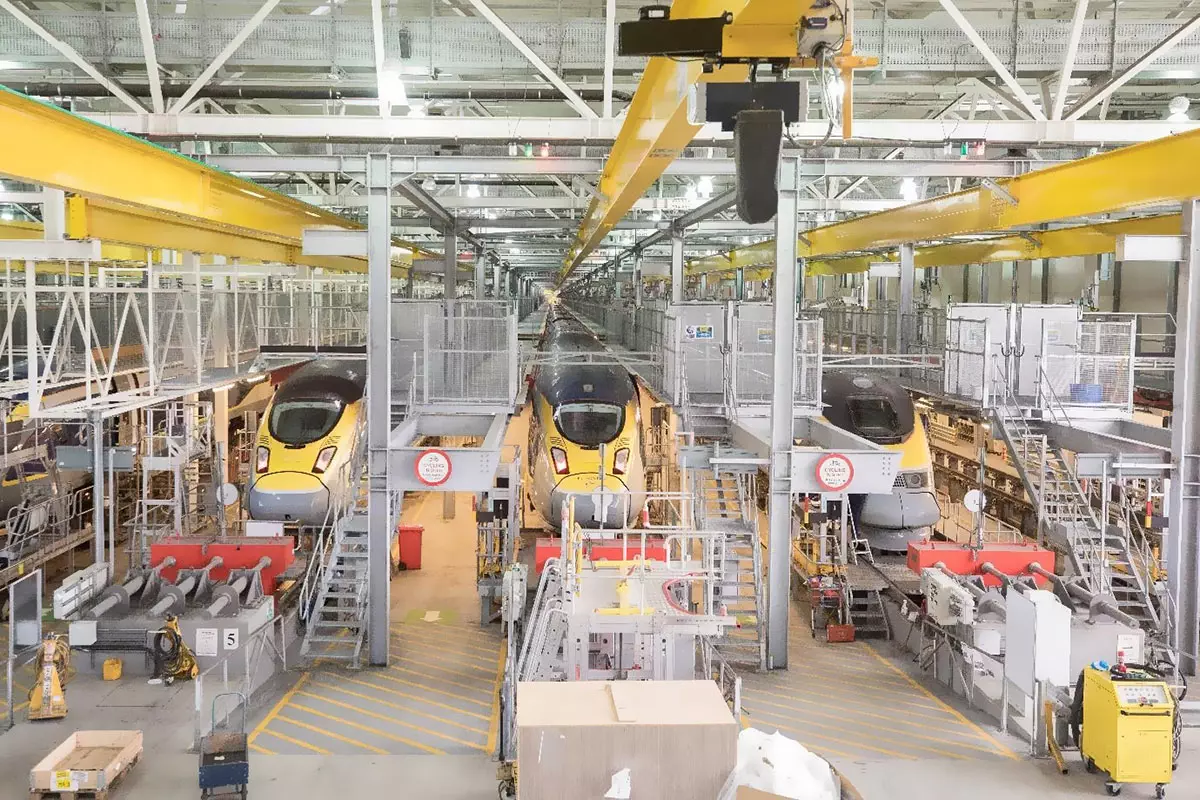
Eurostar und Snap-on Industrial feiern 10 Jahre Partnerschaft.
Alles begann im Jahr 2013. Eurostar kam zu Snap-on, um einige industrielle elektronische Drehmomentschlüssel von ControlTech zu erwerben, und wollte neben anderen hochwertigen, spezialisierten und kalibrierten Werkzeugen auch Optionen für die Steuerung am Einsatzort erkunden.
Eine sorgfältige Prüfung der verfügbaren Optionen führte dazu, dass sich Eurostar für die automatischen Werkzeugsteuerboxen, oder kurz ATCs, von Snap-on entschied. Diese benutzerfreundliche Option würde sich für ihre Endbenutzer als intuitive Lösung erweisen und sich nahtlos in die bestehenden Systeme des Unternehmens integrieren lassen.
Es war der Beginn einer Partnerschaft, die mittlerweile über ein Jahrzehnt andauert – eine Beziehung, die sich zu weit mehr als nur einem Kunden- und Lieferantenverhältnis entwickelt hat – sie ist zu einer Geschäftspartnerschaft geworden.
Eurostar installierte 2014 sein erstes Snap-on-ATC in seiner Drehgestell-Absetzanlage. Eine Tatsache, auf die Eurostar sehr stolz ist, da sie als erstes Eisenbahnunternehmen weltweit das Snap-on-ATC-System eingeführt haben. Der Standort wurde ausgewählt, da die Umgebung vor Ort am härtesten ist. Die Arbeit ist schwer und schmutzig, und die Temperaturen können stark schwanken, da die Hallentore während der gesamten Dauer der Arbeit offen bleiben. Es war der ideale Rahmen, um den Machbarkeitsnachweis zu testen.
Dieser erfolgreiche erste Versuch führte dazu, dass drei weitere ATCs auf Bodenhöhe in der Hauptwartungshalle installiert wurden, um die Einführung der 374-Flotte im Jahr 2015 zu ermöglichen.
Anschließend wurden vier weitere auf den Hochregalbrücken installiert, um Werkzeuge für Arbeiten an der Dachausrüstung der neuen Flotte bereitzustellen, und ein weiteres ATC wurde außerhalb des Büros des Teamleiters installiert, um Schlüssel und seltene Werkzeuge unterzubringen, die anderswo nicht zu finden waren. Bis Ende 2016 waren im Depot insgesamt neun ATCs im Einsatz.
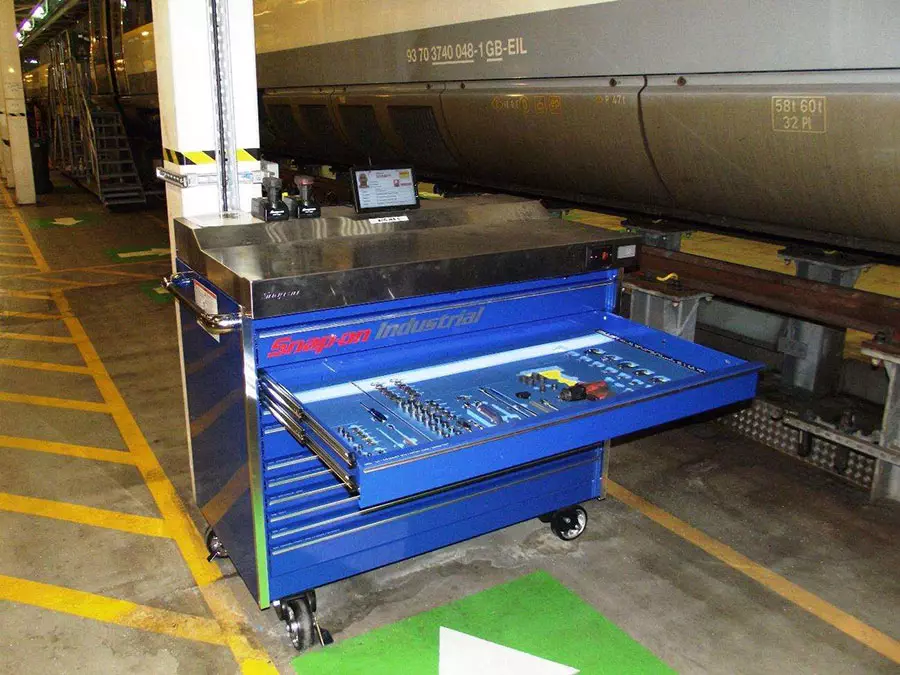
ATC befindet sich außerhalb der Büros der Teamleiter und enthält Schlüssel und nicht standardmäßige Werkzeuge
Acht Jahre später verfügt Eurostar nun über 25 ATC-Boxen – ein Beweis für den Erfolg des Programms, die Erweiterung der 374-Flotte und Depotänderungen. Das Unternehmen ist heute einer der größten Anwender des Snap-on Automated Tool Control-Systems in Großbritannien.
Tatsächlich wird in Kürze ein 26. ATC eingeführt, und es gibt Diskussionen über die Einführung von Boxen in ganz Europa, damit die gesamte Werkzeugverwaltung von Eurostar über eine einzige Software verwaltet werden kann: L5 Connect.
Eurostar hat seit der Einführung der ATCs vor zehn Jahren drei Hauptvorteile gesehen:
- Reduzierte Abhängigkeit von Teamkäfigen
- Verbessertes Werkzeugmanagement und Reduzierung von Werkzeugverlusten
- Höhere Effizienz – durch strategische Point-of-Use-Werkzeuge
Das Depot verfügte über mehr als 20 Ingenieurteams, von denen jedes über einen grundlegenden Werkzeugsatz für persönliche Probleme verfügte. Sie hatten außerdem Zugang zu zwei Team-Werkzeugkäfigen, die sich beide an verschiedenen Standorten innerhalb der 450 Meter langen Halle befanden. Die Einführung von ATCs ermöglichte eine bessere Werkzeugverfügbarkeit am Einsatzort, wodurch der Bedarf an diesen Teamkäfigen um 50 % reduziert wurde und sichergestellt wurde, dass alle kalibrierten und speziellen Werkzeuge rund um die Uhr von den ATCs aus zugänglich sind.
Da mehrere Teams in einem Sieben-Tage-Schichtmuster mit sieben Tagen Pause arbeiteten, waren die in diesen Teamkäfigen eingeschlossenen Werkzeuge sechs Monate im Jahr unzugänglich. Dies war eine Verschwendung der Werkzeugausgaben des Unternehmens und bedeutete, dass keine zwei Teams über den gleichen Werkzeugbestand verfügten. Bis zur Einführung der ATCs kannte niemand bei Eurostar den genauen Inhalt aller Team-Werkzeugkäfige.
ATCs haben zu einer Verhaltensänderung innerhalb des Teams geführt, da sich Einzelpersonen jetzt weniger auf persönliche und Team-Tools verlassen und stattdessen einfach zur nächstgelegenen ATC-Box gehen, um die Tools zu erhalten, die sie benötigen.
Gerade bei Reparaturen und ungeplanten Eingriffen hat diese neue Arbeitsweise zu einer großen Zeitersparnis geführt. Ingenieure können sich schnell einen Druck- oder Meßgenerator von dem nächstgelegenen ATC holen, anstatt quer durch das Depot laufen zu müssen, um zu ihrem Teamkäfig zu gelangen.
Sobald die ATC-Boxen installiert sind, muss der Benutzer lediglich seinen Firmenausweis an den Kartenleser halten und die Toolbox greift automatisch auf das Benutzerkonto zu und entsperrt die Box. Dieser Komfort wurde von den Endbenutzern bei Eurostar allgemein gelobt.
Jedes Werkzeug im Besitz des Unternehmens kann jetzt über L5 Connect verfolgt werden. Diese Software zeichnet sofort auf, wenn ein Werkzeug aus dem ATC entfernt wird, um es zu verwenden, zu kalibrieren oder zu reparieren. Defekte Werkzeuge können auch hervorgehoben werden, indem über den Touchscreen der Box eine Ersatz- oder Reparaturanfrage gestellt wird. Dieses innovative System wurde von unabhängigen Prüfern gelobt, die die Werkzeugverfolgung und -verwaltung von Eurostar bewerteten.
Bei der Einführung von L5 Connect arbeitete das Snap-on-Team eng mit dem IT-Team von Eurostar zusammen, um sicherzustellen, dass der Rollout problemlos umgesetzt werden konnte. Die beiden Teams haben sich ausnahmslos zweimal pro Woche verbunden – und das auch weiterhin, nachdem die L5 Connect-Software installiert ist.
Scott Seacombe, Wirtschaftsingenieur und ATC-Projektmanager, sagte: „Die ATC-Software ist ein absolutes Juwel. Es ist erstaunlich, wie nützlich es sein kann, einen genauen Transaktionsverlauf für Werkzeuge zu führen, und die Bilder, die von jeder geöffneten und geschlossenen Schublade erzeugt werden, können äußerst beeindruckend sein.“ hilfreich.“
Die Partnerschaft zwischen Eurostar und Snap-on hat sich im Laufe der Jahre zu einer echten Zusammenarbeit entwickelt. Eurostar kommt mit seinen dringendsten Problemen zu Snap-on und das Team arbeitet daran, Lösungen zu finden, sei es bei der Entwicklung eines maßgeschneiderten Werkzeugs oder der Einführung neuer Produkte wie Einkaufswagen, um die spezifischen Bedürfnisse von Eurostar zu erfüllen.
Die Langlebigkeit der Beziehung ist ein Beweis dafür, dass die Investition in ATCs zu greifbaren Ergebnissen für Eurostar geführt hat. Jede neue Iteration der ATC-Boxen – derzeit Generation 4 – hat alle Probleme beseitigt, die das Team möglicherweise hatte, und das Snap-on-Account-Management-Team wurde auf allen Ebenen, vom Management bis zu den Ingenieuren, vollständig in das gesamte Eurostar-Engineering-Team integriert der Boden.
Es handelt sich um eine gegenseitige Beziehung, die das Beste aus beiden Partnern herausholt – und die mit dem Wachstum von Eurostar und der Weiterentwicklung der Werkzeugverwaltungssysteme von Snap-on im Laufe der Zeit immer stärker werden wird. Auf das nächste Jahrzehnt.
UNTERNEHMENSPROFIL
Seit 1920 ist Snap-on Industrial ein weltweit führender Spezialist für Werkzeuglösungen mit unübertroffener Expertise bei der Bereitstellung maßgeschneiderter Lösungen für eine Vielzahl von Industriesektoren, darunter Rohstoffgewinnung, Verteidigung, Luftfahrt, Bauwesen sowie Fertigung, Schienenverkehr und Lebensmittelproduktion.
Snap-on Industrial bietet Unternehmen strategische Vorteile bei der Bewältigung der Herausforderung der Rentabilitätssteigerung durch reduzierte Ausfallzeiten, erhöhte Produktivität und Kostenkontrolle.